COMMONWEALTH OF MASSACHUSETTS
SECTION 721.560
CONSTRUCTION NOISE CONTROL
Section 1: Description
Section 2: Materials
Section 3: Construction Methods
Section 4: Compensation
Tables and Figures
1.01 GENERAL
A. The intent of this Section is to minimize construction noise within
construction areas, lay-down areas, and communities adjacent to the
construction site. To this end, the Contractor and all subcontractors,
suppliers, and vendors, are required to comply with all applicable noise
regulations, specification requirements, and the noise level limits
specified herein. This Section supplements the requirements of Division I,
Subsection 7.01E. Refer also to Division I, Subsection 8.06, Limitation of
Operations, Subsection 7.27, Safety, and Exhibit I-J, Mitigation
Requirements
B. This Section specifies requirements for Noise Control Plans, a Noise
Monitoring Plan, noise monitoring prior to and during construction,
response to community complaints, and equipment certification. All
requirements of this Section shall be overseen by an approved Acoustical
Engineer employed by the Contractor.
C. The Contractor shall use equipment with efficient noise-suppression
devices and employ other noise abatement measures such as enclosures and
barriers necessary for the protection of the public. In addition, the
Contractor shall schedule and conduct operations in a manner that will
minimize, to the greatest extent feasible, the disturbance to the public
in areas adjacent to the Work and to occupants of buildings in the
vicinity of the Work.
D. In no case shall the restrictions identified in this Section limit
the Contractor's responsibility for compliance with all Federal, state,
and local safety ordinances and regulations.
E. Related Work specified elsewhere:
Section 850.001 Traffic Control for Construction and Maintenance
Operations.
1.02 TERMS USED
A. Noise is any audible sound which has the potential to annoy
or disturb humans, or to cause an adverse psychological or physiological
effect on humans.
B. Daytime refers to the period from 7 AM to 6 PM local time
daily, except Sundays and Federal holidays.
C. Evening refers to the period from 6 PM to 10 PM local time
daily, except Sundays and Federal holidays.
D. Nighttime refers to the period from 10 PM to 7 AM local time
daily, as well as all day Sunday and Federal holidays.
E. Noise-Sensitive Locations shall mean locations where
particular sensitivities to noise exist, such as residential areas,
institutions, hospitals, and parks.
F. Nuisance Noise refers to sound levels that annoy or disturb a
reasonable person of normal sensitivities, but do not exceed the noise
limits specified herein.
G. Lot-line refers to the line separating a parcel of land from
another parcel or from the street.
H. Background Noise shall be defined as the measured ambient
noise level associated with all existing environmental, transportation,
and community noise sources in the absence of any audible construction
activity.
I. dBA shall be defined as the sound level (in decibels
referenced to 20 micro-pascals) as measured using the A-weighting network
on a sound level meter, in accordance with ANSI S1.4 Standards.
J. Lmax shall be defined as the maximum measured sound level at
any instant in time.
K. Leq shall be defined as the equivalent sound level, or the
continuous sound level that represents the same sound energy as the
varying sound levels, over a specified monitoring period.
L. L10 shall be defined as the sound level exceeded 10 percent
of the time for a specified monitoring period.
M. Slow specifies a time constant or 1 second for the
root-mean-square (RMS) detector used by a sound level meter, in accordance
with ANSI S1.4 Standards.
N. Impact noise is noise produced from impact or devices with
discernible separation in sound pressure maxima. Examples for impact
equipment include, but are not limited to; blasting, clam shovel or chisel
drops, pavement breakers, jackhammers, hoe rams, mounted impact hammers,
and impact pile drivers ( but not vibratory pile drivers). Table 2
specifies types of equipment which are considered to emit impact or
continuous noise.
1.03 SUBMITTALS
A. Submit the name, address, and qualifications of the Acoustical
Engineer, as specified in Article 1.05 of this Section, for review and
acceptance as required by Division I, Subsection 5.02. This submittal is
required prior to preparing the Noise Monitoring and Noise Control Plans,
performing any noise monitoring, or initiating any construction activity.
B. Submit the Noise Monitoring Plan prior to construction, as specified
in Article 1.06 of this Section, for review and acceptance as required by
Division I, Subsection 5.02. The Noise Monitoring Plan shall also contain
background noise readings at all the receptor locations identified in
Table 3 and Figure 1 of this Section, as described in Article 3.01.B of
this Section.
C. Submit a current laboratory calibration conformance certificate for
the noise monitoring equipment, as specified in Article 2.02 of this
Section, prior to performing any noise level monitoring. Submit updated
certificates following subsequent yearly calibrations, or upon completion
of repairs to the instrument, for the duration of this Contract.
D. Submit a Noise Control Plan every 6 months as specified in Article
1.07 of this Section, for review and acceptance as required by Division I,
Subsection 5.02. The first of these submittals is required prior to
construction and no later than 60 Days after Notice -to-Proceed.
An updated Noise Control Plan submittal is required every 6 months after
the date that the initial Noise Control Plan was due, or more frequently
as Work conditions or Work hours change substantively from the conditions
described in a previously approved Noise Control Plan.
E. Submit Noise Measurement Reports on a weekly basis during
construction as specified in Article 3.01 and 3.02 of this Section. The
weekly reports shall include all noise level measurements taken during the
previous week, including construction compliance monitoring and any
required complaint response investigations.
F. Submit all applicable Equipment Noise Compliance Certification
measurements for review and acceptance in accordance with Article 3.05 and
Figure 5 of this Section. Once accepted by the Engineer, Equipment Noise
Certificates will remain valid for not more than 6 month, or less if
subsequent field inspection noise compliance measurements indicate that a
given piece of equipment no longer meets it respective 50 ft emission
limit as provided in Table 2 of this Section.
G. Submit shop and working drawings, computations, material data, and
other descriptions for abatement measures identified in the Noise Control
Plan or used as Temporary Noise Barriers, Acoustical Barrier Enclosures,
or Noise Control Curtains as specified in Articles 2.04, 2.05, 2.06 of
this Section. Drawings and computations shall be stamped by a Registered
Professional Engineer of the Commonwealth of Massachusetts as required by
Division I, Subsection 5.02.
1.04 CONSTRUCTION LIMITATIONS
A. Noise Levels
- 1. Daytime, evening, and nighttime construction noise levels at
noise-sensitive locations and other noise monitoring locations, as
specified in paragraph 1.06.B.1, shall not exceed the lot-line noise
limits specified in Table 1. The lot-line criteria shall apply to all
points on a given lot-line of an affected receptor.
2. Equipment and associated equipment operating under full load that
meets the requirements as specified in Article 1.08 of this Section
shall not exceed the Lmax noise limits specified in Table 2. The 50-foot
noise emission limits specified in Table 2 shall apply to the entire
operation in which the equipment is engaged. Table 2 also provides
distinction as to which equipment is considered to emit impact or
continuous noise.
3. Work shall be performed in a manner to prevent nuisance conditions
such as noise which exhibits a specific audible frequency or tone (e.g.,
backup alarms, unmaintained equipment, brake squeal) or impact noise
(e.g., jackhammers, hoe rams). The Engineer will make any final
interpretation concerning whether or not nuisance noise conditions
exist. The Engineer has the authority to stop the Work until nuisance
noise conditions are resolved, without additional time or compensation
for the Contractor.
4. Work performed by the Contractor in the absence of an approved Noise
Monitoring Plan, Noise Control Plan, and Equipment Noise Certificates
shall be done solely at the discretion of the Engineer. Any Work
stoppages ordered by the Engineer as a result of unacceptable noise
conditions shall not be grounds for any compensation nor claims from the
Contractor.
B. Equipment Operations
- 1. The use of impact pile-drivers shall be prohibited during evening
and nighttime hours (i.e. 6 PM to 7 AM as defined in Article 1.02).
2. Vibratory sheet pile driving shall be prohibited during the
nighttime period (i.e. 10 PM to 7 AM as defined in Article 1.02).
3. All jackhammers, chainsaws, and pavement breakers used on the
construction site shall be enclosed with shields, acoustical barrier
enclosures, or noise barriers as described in an Exhibit at the end of
Division II Special Provisions.
-
4. Use of all impact devices, including hoe rams, jackhammers,
chiseling devices, and pavement breakers, shall be prohibited during the
nighttime hours (i.e. 10 PM to 7 AM). Any necessary use of impact
devices between 10 PM and 7 AM shall be reviewed by the Engineer in
advance and allowed as an exception only upon sufficient justification.
-
5. Contractors shall use approved CA/T haul routes to minimize
noise at residential and other sensitive noise receptor sites.
6. All equipment with backup alarms operated by the Contractor,
vendors, suppliers, and subcontractors on the construction site shall be
equipped with either audible self-adjusting ambient-sensitive backup
alarms or manually-adjustable alarms. The ambient-sensitive alarms shall
automatically adjust to a maximum of 5 dBA over the surrounding
background noise levels. The manually-adjustable alarms shall be set at
the lowest setting required to be audible above the surrounding noise.
Installation and use of the alarms shall be consistent with the
performance requirements of the current revisions of Society of
Automotive Engineering (SAE) J994, J1446, and OSHA regulations, and as
described in an Exhibit at the end of Division II Special Provisions.
7. Per Massachusetts State regulations, engine idling for trucks is
limited to 5 minutes maximum.
1.05 ACOUSTICAL ENGINEER
A. The Acoustical Engineer identified in this Article shall oversee all
requirements of this Section. These include the preparation and
implementation of the Noise Monitoring Plan and Noise Control Plans, the
Equipment Noise Certifications, and the construction and complaint
response noise monitoring.
B. The Acoustical Engineer shall have the following minimal
qualifications:
- 1. Bachelor of Science or higher degree from a qualified program in
engineering, physics, or architecture offered by an accredited
university or college, and five years experience in noise control
engineering and construction noise analysis; or current enrollment as a
full Member or Board-certified Member in the Institute of Noise Control
Engineering (INCE).
2. Demonstrated substantial and responsible experience in preparing and
implementing construction noise controls and monitoring plans on
construction projects conducted in an urban setting, calculating
construction noise levels, and designing and overseeing the
implementation of construction noise abatement measures.
C. If at any point, in the judgement of the Engineer, the quality of the
Acoustical Engineers submittals proves to be repeatedly
unacceptable, then the Engineer can require the submittal and selection of
an alternative Acoustical Engineer meeting the requirements in this
Article.
1.06 NOISE MONITORING PLAN
A. The Noise Monitoring Plan describes the noise monitoring and
reporting procedure to be used during construction. The Plan shall be
prepared by and bear the signature of the Acoustical Engineer and shall be
submitted to the Engineer as specified in paragraph 1.03.B. Noise
generating equipment shall not be operated prior to acceptance of the
Noise Monitoring Plan.
B. The Noise Monitoring Plan shall identify and describe the following
in detail:
- 1. The receptor locations where noise monitoring will be performed.
Include locations identified in Table 3 and shown in Figure 1 and others
as appropriate to effectively monitor noise conditions during
construction. Include sketches of all locations.
- 2. The type of noise level measurement device that will be used, as
specified in Article 2.02 of this Section.
- 3. The noise monitoring methods and procedures that will be used, as
specified in Article 3.01 of this Section.
- 4. The data reporting method that will be used, as specified in
Article 3.02 of this Section.
- 5. The response procedure and actions to be taken for any lot-line or
equipment noise level that exceeds the noise limits specified in Article
1.04 of this Section. The response procedure may include, but not be
limited to, use of noise reduction materials and equipment listed in
Article 2.03 and methods listed in Article 3.03.
- 6. The complaint response and resolution procedures, as specified in
Article 3.06 of this Section.
- 7. Documentation from noise monitor manufacturer warranting that the
specific equipment is "Y2K Compliant".
C. The Noise Monitoring Plan shall also contain the Contractors
submittal of background noise measurements performed in accordance with
Article 3.01.B of this Section (provided by the Engineer in Table 5)
along with the corresponding lot-line noise criteria limits computed in
accordance with Table 1 of this Section for all the noise receptor
locations identified in Table 3 and Figure 1 of this Section.
1.07 NOISE CONTROL PLAN
A. The Noise Control Plan describes the procedure for predicting
construction noise levels prior to performing construction activities and
describes the noise reduction measures required to meet the noise level
limitations and minimize nuisance noise conditions. The Plan shall be
prepared by and bear the signature of the Acoustical Engineer and shall be
submitted to the Engineer as specified in paragraph 1.03.D. Noise
generating equipment shall not be operated prior to acceptance of the
applicable Noise Control Plan. The initial Noise Control Plan is required
no later than 60 Days after Notice-to-Proceed. Updated Noise Control Plans
shall be resubmitted every six months thereafter, or whenever the
Construction activities or the construction Work hours have changed, as
specified in paragraph 1.03.D.
B. The Plan shall include:
- Contract-specific noise control commitments made previously by the
Project as referenced in this Section.
- A description of the anticipated construction activities.
- An inventory of construction equipment and associated noise levels
using Part A of the Noise Control Plan Form in Figure 2. The following
information is required:
- a. Column (a): Code to identify equipment for sketches
and equipment certification procedures.
- b. Column (b): Appropriate equipment category from Table
2.
- c. Column (c): Equipment manufacturer and model.
- d. Column (d): Unique identifier (ID), such as
registration number.
- e. Column (e): Horsepower rating of the equipment.
- f. Column (f): Equipment noise emission limit from Table
2.
- g. Column (g): Estimated noise level at 50 feet. If
greater than the limit specified in Table 2, noise reduction
measures will need to be included.
- h. Column (h): Estimated date of first use on site.
- i. Column (i): Estimated date of last use on site.
- j. Column (j): Expected use; circle D for daytime, E for
evening, N for nighttime use.
- 4. Noise Level Calculations
Perform calculations to predict lot-line construction noise during
applicable daytime, evening, and nighttime periods. The calculations
shall be made for noise monitoring locations as specified in paragraph
1.06.B.1 where noise emitted by all applicable equipment will cause the
greatest noise level for each type of land use for a given time period.
The Contractor shall provide the results on Part B of the Noise Control
Plan Form in Figure 3 with calculations included below the results, and
with the locations for the calculations indicated on the site sketch.
The noise level calculation procedure shall be as follows:
- a. Calculate Lmax:
1. Calculate the maximum equipment noise level at the closest
point on the lot-line for each item of equipment using the
following equation:
Lmax(equipment) = E.L. - 20 log (D/50)
where:
E.L. is the estimated equipment noise emission level at 50
feet (Figure 2, column g or from Table 2 of this Section) in
dBA.
D is the distance from the equipment to the closest point
on the lot-line in feet, but shall not be less than 50 feet.
2. Whereas the maximum noise level produced by each piece of
equipment may not occur simultaneously, obtain the overall
maximum construction noise level at the lot-line from the
loudest single piece of equipment as follows:
Lmax(overall) = MAX [Lmax(equipment)]
b. Calculate Leq:
1. Calculate Leq at the closest point on the lot-line for each
item of equipment using the following equation:
Leq(equipment)= E.L. - 20 log (D/50) + 10 log
(U.F.%/100)
where:
E.L. and D are as defined above in Article 1.07.B.4.a.1.
U.F. is the "usage factor", and is used to
time-average the noise levels associated with an operating
piece of equipment. The U.F. is expressed as the percentage
of time that the equipment is operated at full power while
on site. This factor shall be estimated by the Contractor or
the Acoustical Engineer. Guidelines for the selection of
usage factors are provided by the U.S. Environmental
Protection Agency ("Noise From Construction Equipment
and Operations, Building Equipment, and Home Appliances",
U.S. Environmental Protection Agency Report NTID 300.1,
December 31, 1971), or are also provided for use in Table 2
of this Section.
2. Combine the individual contributions of each piece of
equipment to obtain the overall construction Leq at the lot-line
as follows:
Leq(overall) = 10 log S
10 [Leq(equipment)/10]
c. Calculate L10:
Finally, as supported by previous construction noise studies,
calculate the estimated overall L10 by simply adding 3 dBA to
the overall Leq as follows:
L10(overall) = Leq(overall) + 3 dBA
5. Noise Level Limit Calculations
Perform calculations to determine L10 lot-line noise level limits
during applicable daytime, evening, and nighttime periods based on the
background noise level data as specified in Table 1 and Article 3.01 of
this Section. The calculations shall be made for noise monitoring
locations listed in Table 3 of this Section. Background noise levels
and corresponding lot-line noise criteria limits for this contract have
already been established by the Engineer and can be seen in Table 5 of
this Section.
a. Determine the L10 noise level limits for daytime, evening, and
nighttime time periods from Table 1 based on the background L10
noise levels established in accordance with Article 3.01.B of this
Section for each time period (furnished by the Engineer in Table
5).
b. The Lmax noise level limits are absolute limits from Table 1
and do not rely on background conditions.
6. A sketch of the construction site indicating the following:
a. Contract name and number, Contractor's name, date, scale, legend
of symbols, and direction of North.
b. Construction equipment locations, designated by codes used
in Column (a) in Figure 2.
- c. All noise receptor locations near the construction site, as
specified in paragraph 1.06.B.1.
- d. Locations and types of noise reduction measures that may be
required to demonstrate compliance with noise limits as specified in
Article 1.04 of this Section.
7. A summary table listing the anticipated unmitigated and, if
warranted, mitigated construction noise levels shall be provided for all
the noise receptor locations (per Article 1.06.B.1.). Each receptors
appropriate lot-line criteria limits (from Table 1) shall also be
referenced in the table.
8. A description of noise reduction measures, if necessary, to meet
the lot-line and equipment noise level limitations as specified in
Tables 1 and 2. The noise reduction measures may include, but not be
limited to, the noise reduction materials and equipment listed in
Article 2.03 and noise reduction methods listed in Article 3.03 of this
Section. If noise reduction measures are required, re-calculate the
noise levels at the lot-line of the noise monitoring location using the
anticipated noise reduction measures and submit the results in Figure 3.
9. Where excessive noise levels are anticipated, noise mitigation
measures must be proposed. The beneficial noise reducing effects of the
mitigation measures must be quantitatively predicted, and compliance
with the specified noise limits in Table 1 must be demonstrated in the
resulting predicted mitigated noise levels.
10. Calculations for noise barrier performance design predictions shall
use the "path-length-difference" method involving fresnel
numbers.
11. Any drawings, sketches and suitable calculations which demonstrate
anticipated noise reduction benefits. Submit shop and working drawings,
computations, materials data, and other descriptions as specified in
paragraph 1.03.G.
1.08 EQUIPMENT NOISE CERTIFICATION
A. The construction equipment to be certified includes any equipment of
the types listed in Table 2 brought on-site. Noise emission limits in
Table 2 shall apply to Contractor and subcontractor equipment.
B. All construction equipment shall be tested using the procedures
specified in Article 3.05 of this Section to ensure compliance with
equipment Lmax noise limits in Table 2. The equipment noise certification
shall be overseen by the Acoustical Engineer and certificates shall be
submitted to the Engineer as specified in paragraph 1.03.F.
C. Equipment shall be tested every 6 months while in use and shall also
be subject to periodic compliance testing whenever evidence of
non-compliance is apparent. Testing shall be performed as described in
Article 3.05 of this Section.
D. Equipment without a currently valid noise certification on file with
the Engineer, or equipment that fails its random noise compliance test
(i.e. exceeds the 50 ft emission limits in Table 2) shall be required to
cease operation until adequate mitigation measures can be implemented.
2.01 GENERAL
A. All equipment and materials specified in this part will remain the
property of the Contractor or Contractor's subcontractors, vendors, and
suppliers, as applicable.
2.02 NOISE MONITORING EQUIPMENT
A. All noise measurements shall be performed with an instrument that is
in compliance with the criteria for a Type 1 (Precision) or Type 2
(General Purpose) Sound Level Meter as defined in the current revision of
ANSI Standard S1.4.
B. The sound level meter shall be capable of measuring dBA noise levels
and operating on the "slow" response setting.
C. Sound level meters shall be capable of measuring and displaying Lmax
and L10 over 20 minute intervals in the field without the need for
post-processing of data.
D. All sound level meters, microphones, and calibrators shall undergo
certified laboratory calibration conformance testing at least once a year.
The calibration certificate shall be submitted to the Engineer as
specified in paragraph 1.03.C.
E. The sound level meter shall be on-site and readily accessible at all
times.
F. All noise monitoring equipment must be documented as being "Y2K
Compliant" to avoid any problems associated with the year 2000
programming issues.
2.03 NOISE REDUCTION MATERIALS AND EQUIPMENT
A. Noise reduction materials may be new or used. Used materials shall be
of a quality and condition to perform their designed function.
B. Noise reduction equipment and materials may include, but not be
limited to:
- 1. Shields, shrouds, or intake and exhaust mufflers.
- 2. Noise-deadening material to line hoppers, conveyor transfer
points, storage bins, or chutes.
- 3. Noise barriers using materials consistent with the Temporary Noise
Barrier materials specified in Article 2.04 of this Section.
- 4. Noise curtains using materials consistent with the Noise Control
Curtains materials specified in Article 2.06 of this Section.
C. All equipment with backup alarms operated by the Contractor, vendors,
suppliers, and subcontractors on the construction site shall be equipped
with either audible self-adjusting ambient-sensitive backup alarms or
manually-adjustable alarms. The ambient-sensitive alarms shall
automatically adjust to a maximum of 5 dBA over the surrounding background
noise levels. The manually-adjustable alarms shall be set at the lowest
setting required to be audible above the surrounding noise. Installation
and use of the alarms shall be consistent with the performance
requirements of the current revisions of Society of Automotive Engineering
(SAE) J994, J1446, and OSHA regulations, and as described in an Exhibit at
the end of Division II Special Provisions.
D. All equipment used on the construction site, including jackhammers
and pavement breakers, shall have exhaust systems and mufflers that have
been recommended by the manufacturer as having the lowest associated
noise.
E. The local power grid shall be used wherever feasible to limit
generator noise. No generators larger than 25 KVA shall be used and, where
a generator is necessary, it shall have maximum noise muffling capability
and meet the noise emission limits specified in Table 2.
2.04 TEMPORARY NOISE BARRIERS
A. Temporary barriers shall be constructed of 3/4-inch Medium Density
Overlay (MDO) plywood sheeting, or other material of equivalent utility
and appearance having a surface weight of 2 pounds per square foot or
greater. The temporary noise barriers shall have a Sound Transmission
Class of STC-30, or greater, based on certified sound transmission loss
data taken according to ASTM Test Method E90.
B. The temporary barriers shall be lined on one side with glass fiber,
mineral wool, or other similar noise curtain type noise-absorbing material
at least 2-inches thick and have a Noise Reduction Coefficient rating of
NRC-0.85, or greater, based on certified sound absorption coefficient data
taken according to ASTM Teat Method C423.
C. The materials used for temporary barriers shall be sufficient to last
through the duration of construction for this Contract, and shall be
maintained in good repair.
D. Construction Details
- 1. Barrier panels shall be attached to support frames constructed in
sections to provide a moveable barrier utilizing the standard "Temporary
Precast Concrete Median Barrier" for the Project, as shown on
Standard Drawing SD-H-401 and SD-H-403 for Construction Barricade, or
other supports designed to withstand 80 mph wind loads plus a 30 percent
gust factor.
2. When barrier units are joined together, the mating surfaces of the
barrier sides shall be flush with each other. Gaps between barrier
units, and between the bottom edge of the barrier panels and the ground,
shall be closed with material that will completely fill the gaps, and be
dense enough to attenuate noise.
3. The barrier height shall be designed to break the line-of-sight and
provide at least a 5 dBA insertion loss between the noise producing
equipment and the upper-most story of the receptor(s) requiring noise
mitigation. If for practicality or feasibility reasons, which are
subject to the review and approval of the Engineer, a barrier can not be
built to provide noise relief to all stories, then it must be built to
the tallest achievable height.
E. Prefabricated acoustic barriers are available from various vendors.
An equivalent barrier design can be submitted as specified in paragraph
1.03.G in lieu of the plywood barrier described above.
2.05 ACOUSTICAL BARRIER ENCLOSURES
A. Materials
- 1. The acoustical barrier enclosure shall consist of durable,
flexible composite material featuring a noise barrier layer bonded to
sound-absorptive material on one side.
2. The noise barrier layer shall consist of rugged, impervious material
with a surface weight of at least one pound per square foot. The sound
absorptive material shall include a protective face and be securely
attached to one side of the flexible barrier over the entire face.
3. The acoustical material used shall be weather and abuse resistant,
and exhibit superior hanging and tear strength during construction. The
material shall have a minimum breaking strength of 120 lb/in. per FTMS
191 A-M5102 and minimum tear strength of 30 lb/in. per ASTM D117. Based
on the same test procedures, the absorptive material facing shall have a
minimum breaking strength of 100 lb/in. and a minimum tear strength of 7
lb/in.
4. The acoustical material shall be corrosion resistant to most acids,
mild alkalies, road salts, oils, and grease.
5. The acoustical material shall be fire retardant and be approved by
the City of Boston Fire Department prior to procurement. It shall also
be mildew resistant, vermin proof, and non-hygroscopic.
6. The acoustical material shall have a Sound Transmission Class of
STC-25 or greater, based on certified sound transmission loss data taken
according to ASTM Test Method E90. It shall also have a Noise Reduction
Coefficient rating of NRC-0.70 or greater, based on certified sound
absorption coefficient data taken according to ASTM Test Method C423.
7. The Contractor shall submit the name of the manufacturer, properties
of the material to be furnished, and two one-foot square samples to the
Engineer for review prior to submittal of design and detailed
engineering as specified in paragraph 1.03.G.
B. Construction Details
- 1. The acoustical barrier enclosure shall be designed similar to the
example shown in Exhibit II-C, "Construction Noise Control
Specification and Guidelines".
2. The acoustical material shall be installed in vertical and
horizontal segments with the vertical segments extending the full
enclosure height. All seams and joints shall have a minimum overlap of 2
inches and be sealed using double grommets. Construction details shall
be performed according to the manufacturer's recommendations.
3. The Contractor shall be responsible for the design, detailing, and
adequacy of the framework and supports, ties, attachment methods, and
other appurtenances required for the proper construction of the
acoustical barrier enclosure.
4. The design and details for the acoustical noise barrier enclosure
framework and supports shall be prepared and stamped by a Registered
Professional Engineer licensed in the Commonwealth of Massachusetts. The
Contractor shall submit the design and detailed engineering drawings to
the Engineer as specified in paragraph 1.03.G.
2.06 NOISE CONTROL CURTAINS
A. Materials
- 1. The noise control curtain shall consist of durable, flexible
composite material featuring a noise barrier layer bonded to
sound-absorptive material on one side. The noise barrier layer shall
consist of a rugged, impervious material with a surface weight of at
least one pound per square foot. The sound absorptive material shall
include a protective face and be securely attached to one side of the
flexible barrier over the entire face.
2. The noise curtain material used shall be weather and abuse
resistant, and exhibit superior hanging and tear strength during
construction. The curtains noise barrier layer material shall have
a minimum breaking strength of 120 lb/in. per FTMS 191 A-M5102 and
minimum tear strength of 30 lb/in. per ASTM D117. Based on the same test
procedures, the noise curtain absorptive material facing shall have a
minimum breaking strength of 100 lb/in. and a minimum tear strength of 7
lb/in.
3. The noise curtain material shall be corrosion resistant to most
acids, mild alkalies, road salts, oils, and grease. It also shall be
mildew resistant, vermin proof, and non-hygroscopic.
4. The noise curtain material shall be fire retardant and be approved
by the City of Boston Fire Department prior to procurement.
5. The noise control curtain shall have a Sound Transmission Class of
STC-30 or greater, based on certified sound transmission loss data taken
according to ASTM Test Method E90. It shall also have a Noise Reduction
Coefficient rating of NRC-0.85 or greater, based on certified sound
absorption coefficient data taken according to ASTM Test Method C423.
6. The Contractor shall submit the name of the manufacturer, properties
of the material to be furnished, and two one-foot square samples to the
Engineer for review prior to submittal of the design and detailed
engineering drawings as specified in paragraph 1.03.G.
B. Construction Details
- 1. The noise control curtains shall be designed such as described in
an Exhibit at the end of Division II Special Provisions, "Construction
Noise Control Specification and Guidelines." The curtains shall be
secured above, at the ground, and at intermediate points by framework
and supports designed to withstand 80 mph wind loads plus a 30 percent
gust factor.
2. The curtains shall be installed in vertical and horizontal segments
with the vertical segments extending the full curtain height to the
ground. All seams and joints shall have a minimum overlap of 2 inches
and be sealed using Velcro or double grommets spaced 12 inches on
center. Curtains shall be fastened to framework and guardrails with wire
cable 12 inches on center. Construction details shall be performed
according to the manufacturer's recommendations.
3. The curtain height shall be designed to break the line-of-sight and
provide at least a 5 dBA insertion loss between the noise producing
equipment and the upper-most story of the receptor(s) requiring noise
mitigation. If for practicality or feasibility reasons, which are
subject to the review and approval of the Engineer, a curtain system can
not be built to provide noise relief to all stories, then it must be
built to the tallest achievable height.
4. The Contractor shall be responsible for the design, detailing, and
adequacy of the framework and supports, ties, attachment methods, and
other appurtenances required for the proper installation of the noise
control curtains.
5. The design and details for the noise control curtains framework and
supports shall be prepared and stamped by a Registered Professional
Engineer licensed in the Commonwealth of Massachusetts. The Contractor
shall submit the design and detailed engineering drawings to the
Engineer as specified in paragraph 1.03.G.
3.01 NOISE MONITORING METHODS
A. General
- 1. The sound level meter and the acoustic calibrator shall be
calibrated and certified annually by the manufacturer or other
independent certified acoustical laboratory. The sound level meter shall
be field calibrated using an acoustic calibrator, according to the
manufacturer's specifications, prior to and after each measurement.
2. All measurements shall be performed using the A-weighting network
and the "slow" response of the sound level meter.
3. The measurement microphone shall be fitted with an appropriate
windscreen, shall be located 5 feet above the ground, and shall be at
least 5 feet away from the nearest acoustically-reflective surface.
4. Noise monitoring shall not be performed during precipitation or when
wind speeds are greater than 15 mph, unless the microphone is protected
in such a manner as to negate the acoustic effects of rain and high
winds.
B. Background Noise Monitoring
- 1. Background noise measurements (in dBA, slow) shall be collected
for at least 24 hours over two non-consecutive days Monday through
Saturday and one Sunday at noise monitoring receptor locations as
specified in paragraph 1.06.B.1 prior to the start of construction.
Background noise measurements should be performed in the absence of any
contributing construction noise for each of the noise monitoring
receptor locations identified in Table 3 and Figure 1 of this Section.
Background noise L10 levels shall be arithmetically averaged into single
L10 levels defining the background noise for daytime (7 AM - 6 PM),
evening (6 PM - 10 PM), and nighttime (10 PM - 7 AM) time frames,
respectively.
(Background noise measurements for each of the noise monitoring
receptor locations identified in Table 3 and Figure 1 have already been
collected for this contract and are furnished by the Engineer in Table 5
of this Section.)
C. Construction Noise Monitoring
- 1. Noise level measurements shall be taken at each noise-sensitive
location during ongoing construction activities at least once each week
during the applicable daytime, evening, and nighttime period. All other
noise monitoring locations as specified in paragraph 1.06.B.1 shall be
measured at least once each week during the daytime period.
2. The time period for each noise measurement shall be 20 minutes.
3. Construction noise measurements shall coincide with daytime,
evening, and nighttime periods of maximum noise-generating construction
activity, and shall be performed during the construction phase or
activity that has the greatest potential to exceed noise level
limitations as specified in Article 1.04 of this Section. Compliance
noise measurements for the noise limits in Table 1 shall be performed at
a point on a given lot-line which is the closest to the construction
activity.
4. If, in the estimation of the person performing the measurements,
outside sources contribute significantly to the measured noise level,
the measurements shall be repeated with the same outside source
contributions when construction is inactive to determine the ambient
noise level contribution.
5. All measurements shall be taken at the affected lot-line. In
situations where the Work site is within 50 feet of a lot-line, the
measurement shall be taken from a point along the lot-line such that a
50 foot distance is maintained between the sound level meter and the
construction activity being monitored.
-
6. Up to four 24-hour noise monitors shall be maintained at the
lot-line of noise receptor locations and shifted among locations
corresponding to construction activity as directed by the Engineer.
These monitors shall be capable of recording the Lmax and L10 values in
20-minute intervals over 24-hour periods. These monitors shall be
durable and enclosed in weather resistant cases, and located in a manner
that will prevent vandalism. The data shall be downloaded and submitted
as specified by paragraph 1.03.E.
3.02 REPORTING
A. Background, construction, and complaint response noise data shall be
recorded on the Noise Measurements Report Form provided in Figure 4. The
type of measurement shall be noted on the form.
B. 24-hour noise measurements shall be plotted graphically showing L10
and Lmax noise levels vs time along with appropriate lot-line criteria
limits (from Tables 1 and 5) for daytime, evening, and nighttime periods.
C. Provide a sketch or diagram for the exact location of the noise
measurement on the back of Figure 4. Include the location and distance of
the noise measurement in relationship to the noise monitoring location
specified in paragraph 1.06.B.1.
D. During construction and complaint response monitoring, all
construction equipment operating during the monitoring period shall be
identified and the location sketched on the back of Figure 4. The sketch
shall include the distance between the noise measurement location and the
construction equipment.
E. All activities occurring while performing noise measurements shall be
noted in the "Field Notes" area of Figure 4. For example, "auger
banging on ground to clean soil from threads" or "heavy traffic
passing near the sound level meter." In addition, any noise level of
85 dBA or greater requires an explanation.
3.03 NOISE REDUCTION METHODS
A. The Contractor shall use all reasonable efforts to implement noise
reduction methods listed below to minimize construction noise emission
levels and as described or specified under Limiting Unnecessary
Construction Noise in an Exhibit at the end of Division II Special
Provisions. Noise reduction methods shall include, but not be limited to:
3.04 TEMPORARY NOISE BARRIERS
- 1. Use of: 1) concrete crushers or pavement saws for concrete
deck removal, demolitions, or similar construction activity; 2)
pre-auguring pile holes to reduce the duration of impact or vibratory
pile driving; 3) tie to local power grid to reduce the use of
generators.
2. Attaching: 1) intake and exhaust mufflers, shields, or
shrouds; 2) noise-deadening material to inside of hoppers, conveyor
transfer points, or chutes.
3. Maintaining: 1) equipment mufflers and lubrication; 2)
precast decking or plates to avoid rattling; 3) surface irregularities
on construction sites to prevent unnecessary noise.
4. Limiting: 1) the number and duration of equipment idling on
the site; 2) the use of annunciators or public address systems; 3) the
use of air or gasoline-driven hand tools.
5. Configuring, to the extent feasible: 1) the construction
site in a manner that keeps loud equipment and activities as far as
possible from noise-sensitive locations; 2) barrels or signage to detour
traffic away from plated trenches.
6. Scheduling of construction events and limiting usage times
to minimize noise, especially during nighttime hours and near sensitive
abutters.
7. Erecting noise barriers and/or noise curtain systems to
intervene between the noise source and the noise receptor locations.
8. Minimizing noise from the use of backup alarms using
measures that meet OSHA regulations. This includes 1) use of
self-adjusting ambient-sensitive backup alarms, 2) manually-adjustable
alarms on low setting, 3) use of observers, 4) scheduling of activities
so that alarm noise is minimized, 4) construction site access should be
designed such that delivery and dump trucks move through the site in a
forward manner without the need to back up.
9. Using only variable message and sign boards that are solar
powered or connected to the local power grid.
A. General
- 1. The Contractor shall erect temporary noise barriers to mitigate
construction noise at locations specified in the Noise Control Plan or
as directed by the Engineer.
2. The temporary noise barriers shall be readily moveable so that they
may be re-positioned, as necessary, to provide noise abatement for
non-stationary, as well as stationary, processes.
B. Installation, Maintenance, and Removal
- 1. The barriers shall be installed such that the noise-absorptive
surfaces face the construction noise source.
2. The Contractor shall maintain the temporary noise barriers and
repair all damage that occurs, including, but not limited to, keeping
barriers clean and free from graffiti and maintaining structural
integrity. Gaps, holes, and weaknesses in the barriers, and openings
between or under the units, shall be repaired promptly or replaced by
the Contractor with new material.
3. The Contractor shall remove and dispose of the temporary noise
barriers at the end of the Contract or sooner at the direction of the
Engineer.
3.05 EQUIPMENT NOISE CERTIFICATION
A. General
- 1. For each piece of equipment meeting the requirements of paragraph
1.08.A of this Section, complete an Application for Certificate of
Equipment Noise Compliance (Figure 5), which shall be signed by the
Acoustical Engineer.
2. The equipment identification number used for certification shall be
consistent with the identification number used in the Noise Control Plan
(Figure 2).
B. Test Procedures for Construction Equipment
- 1. All engine-powered equipment shall be operated at high idle
(maximum governed rpm) under full-load condition during the test.
2. Portable and mounted impact devices, such as hoe-rams and
jackhammers, shall be tested during the first day of actual operation at
the construction site under maximum load conditions as rated by the
equipment manufacturer.
3. Pile-driving equipment shall be tested under maximum load conditions
as rated by the manufacturer.
4. All noise monitoring equipment specified in Article 2.02 of this
Section shall have a current certificate of calibration sticker affixed
to it.
5. An acoustic calibrator of the type recommended by the sound level
meter manufacturer shall be used prior to and after all measurements.
6. The noise level measurements shall be for a minimum period of 1
minute.
7. If possible, measurements shall be made at 50 feet ± 2 feet
from the front, rear, and right and left sides of the equipment, at a
height of 5 feet above ground level.
8. Measurements made at less than 50 feet, due to space limitations at
the test site, shall be reduced by the values given in Table 4 to
estimate the 50 foot noise level.
9. When confirmatory noise level testing is requested by the Engineer,
the Contractor shall locate and operate the equipment as directed by the
Engineer at the designated site so as to facilitate recording of the
noise level by the Contractor.
C. Compliance
- 1. If the Lmax noise levels (in dBA, slow) obtained during the tests
exceed those specified in Table 2, the Contractor shall promptly modify
or alter such equipment, or substitute other equipment, and retest the
equipment to show compliance with the noise level requirements.
2. Upon compliance, the Contractor shall submit the Equipment Noise
Certificates provided in Figure 5 of this Section to the Engineer for
review, approval, and recording as specified in paragraph 1.03.F.
3. The Certificate of Equipment Noise Compliance will remain valid for
a period of 6 months only. Delays caused by the certification rejection,
and time lost in mitigating the rejected equipment or finding alternate
acceptable equipment, shall not be a basis for any monetary or time
delay claims, or for avoidance of late completion penalties.
3.06 COMPLAINT PROCEDURE
A. The objective of the complaint procedure is to ensure that public and
agency complaints are addressed and resolved consistently and
expeditiously.
B. If the Contractor receives a complaint regarding construction noise,
the Contractor shall immediately notify the Engineer and the Interim
Operations Center (IOC) or successor to the IOC.
C. Upon receipt or notification of a noise complaint from the Engineer,
the Contractor shall promptly perform noise measurements at the
complainant's location during activities representative of the offending
operation. The noise measurements shall be performed using equipment and
methods as specified in Articles 2.02 and 3.01 and reported as specified
in Article 3.02 of this Section. The complaint response noise measurements
shall be immediately submitted to the Engineer as specified in paragraph
1.03.E of this Section.
D. In the event that the measured noise level exceeds allowable limits
as specified in Article 1.04 of this Section, or is resulting in nuisance
conditions, the Contractor shall immediately use noise reduction materials
and methods such as, but not limited to, those described in Article 3.03
to reduce noise levels or to alleviate the nuisance conditions.
3.07 ACOUSTICAL BARRIER ENCLOSURES
A. General
- 1. The Contractor shall erect acoustical barrier enclosures to
mitigate construction noise at locations specified in the Noise Control
Plan as required in Article 1.07, construction drawings, or as directed
by the Engineer.
2. The acoustical barrier enclosures shall be readily moveable so that
they may be repositioned, as necessary, to provide noise abatement for
non-stationary equipment (e.g., jackhammers, chain saws, compressors).
B. Installation, Maintenance, and Removal
- 1. The acoustical enclosure shall be installed such that the
noise-absorptive surfaces face the construction noise source.
2. The Contractor shall maintain the acoustical barrier enclosures and
repair all damage that occurs, including, but not limited to, keeping
barriers clean and free from graffiti and maintaining structural
integrity. Gaps, holes, and weaknesses in the acoustical enclosure, and
openings between or under the panels, shall be repaired promptly or
replaced by the Contractor with new material. Construction Work shall
not proceed until such repairs are made.
3. The Contractor shall remove and dispose of the acoustical enclosure
at the end of the Contract or sooner at the direction of the Engineer.
3.08 NOISE CONTROL CURTAINS
A. General
- 1. The Contractor shall erect noise control curtains to mitigate
construction noise at locations specified in the Noise Control Plan as
required in Article 1.07, construction drawings, or as directed by the
Engineer.
2. Noise control curtains shall particularly be used for short-term
operations (e.g., less than 3 months), or where vehicular or pedestrian
access is required during the day, or as directed by the Engineer.
B. Installation, Maintenance, and Removal
- 1. The noise control curtains shall be installed without any gaps
such that the sound-absorptive side faces the construction activity to
be shielded. The curtains shall be supported by the existing elevated
Expressway, ramps, or other methods identified in the Noise Control
Plan.
2. The Contractor shall maintain the noise control curtains and repair
all damage that occurs, including, but not limited to, keeping barriers
clean and free from graffiti and maintaining structural integrity. Gaps,
holes, and weaknesses in the noise control curtains, and openings
between or under the panels, shall be repaired promptly or replaced by
the Contractor with new material. Construction Work shall not proceed
until such repairs are made.
3. The Contractor shall remove and dispose of the noise control
curtains at the end of the Contract or sooner at the direction of the
Engineer.
4.01 METHOD OF MEASUREMENT
A. The Noise Monitoring Plan and first Noise Control Plan will be
considered incidental to Mobilization (Section 748.001).
B. The 6-month Noise Control Plans, equipment certifications, and
complaint response and weekly construction noise monitoring reports will
be considered incidental to the Construction.
C. Temporary noise barriers installed per Article 3.04 of this Section
will be measured by surface area of one face of the noise barrier wall
with no additions for bracing, supports, and other such projections.
D. Acoustical barrier enclosures constructed per Article 3.07 of this
Section will be measured by surface area of one face of the acoustical
enclosure with no additions for bracing, supports, and other such
projections.
E. Noise control curtains installed per Article 3.08 of this Section
will be measured by surface area of one face of the noise control curtains
with no additions for bracing, supports, and other such projections.
4.02 BASIS OF PAYMENT
A. Payment for the Noise Monitoring Plan and first Noise Control Plan
will be considered part of the payment for Mobilization.
B. Payment for the 6 month Noise Control Plans, equipment
certifications, and complaint response and weekly construction noise
monitoring reports will be considered part of the payment for related
Construction.
C. Payment for temporary noise barriers installed per Article 3.04 of
this Section will be at the Contract unit price per square foot, which
shall be full compensation for constructing, providing, placing,
maintaining, moving, and disposing of temporary noise barrier walls.
D. Payment for the acoustical barrier enclosures constructed per Article
3.07 of this Section will be at the Contract unit price per square foot,
which shall be full compensation for constructing, providing, placing,
maintaining, moving, relocating, and disposing of temporary acoustical
barrier enclosure.
E. Payment for the noise control curtains installed per Article 3.08 of
this Section will be at the Contract unit price per square foot, which
shall be full compensation for constructing, providing, placing,
maintaining, moving, relocating, and disposing of the noise control
curtains.
4.03 PAYMENT ITEM
Line Item |
Item Description |
Item Unit |
721.565 |
Temporary Noise Barrier |
Square Foot |
700.721 |
Acoustical Barrier Enclosure |
Square Foot |
700.722 |
Noise Control Curtains |
Square Foot |
END OF TEXT FOR THIS SECTION
TABLES 1 - 5 AND FIGURES 1 - 5 FOLLOW
TABLE 1. CONSTRUCTION NOISE LOT- LINE LIMITS
(b), (c), (d)
Noise Monitoring
Location Land Use |
L10 Level (dBA, slow)
(whichever is greater) |
Lmax Level (dBA, slow) |
DAYTIME (7 AM to 6 PM) |
|
|
Noise-Sensitive Locations |
75 or Background+5 (a) |
85 (a)
90 (impact equipment) |
Commercial Areas |
80 or Background+5 (a) |
None |
Industrial Areas |
85 or Background+5 (a) |
None |
EVENING (6 PM to 10 PM) |
|
|
Noise-Sensitive Location |
Background+5 |
85 |
Commercial Areas |
None |
None |
Industrial Areas |
None |
None |
NIGHTTIME (10 PM to 7 AM) |
|
|
Noise-Sensitive Locations |
|
|
If Background < 70 dBA |
Background+5 |
80 |
If Background > 70 dBA |
Background+3 |
80 |
Commercial Areas |
None |
None |
Industrial Areas |
None |
None |
NOTES
- (a) Noise from impact equipment is exempt from the L10 requirement,
however is subject to a lot-line Lmax limit of 90 dBA.
- (b) All measurements shall be taken at the affected lot-line. In
situations where the work site is within 50 feet of a lot-line, the
measurement shall be taken from a point along the lot-line such that a
50 foot distance is maintained between the sound level meter and the
construction activity being monitored.
- (c) Lot-line noise limits shall apply to all points along the
receptors lot-line.
- (d) L10 noise readings are averaged over 20 minute intervals. Lmax
noise readings occur instantaneously.
TABLE 2. CONSTRUCTION EQUIPMENT 50 FOOT NOISE EMISSION LIMITS
(a), (b)
Equipment Category |
Lmax Noise Limit
at 50 ft, dBA, slow |
Is Equipment an
Impact Device? (c) |
Acoustic
Usage Factor (d) |
All other equipment > 5 HP |
85 |
No |
50 % |
Auger Drill Rig |
85 |
No |
20 % |
Backhoe |
80 |
No |
40 % |
Bar Bender |
80 |
No |
20 % |
Blasting |
94 |
Yes |
1 % |
Boring Jack Power Unit |
80 |
No |
50 % |
Chain Saw |
85 |
No |
20 % |
Clam Shovel |
93 |
Yes |
20 % |
Compactor (ground) |
80 |
No |
20 % |
Compressor (air) |
80 |
No |
40 % |
Concrete Batch Plant |
83 |
No |
15 % |
Concrete Mixer Truck |
85 |
No |
40 % |
Concrete Pump |
82 |
No |
20 % |
Concrete Saw |
90 |
No |
20 % |
Crane (mobile or stationary) |
85 |
No |
20 % |
Dozer |
85 |
No |
40 % |
Dump Truck |
84 |
No |
40 % |
Excavator |
85 |
No |
40 % |
Flat Bed Truck |
84 |
No |
40 % |
Front End Loader |
80 |
No |
40 % |
Generator (25 KVA or less) |
70 |
No |
50 % |
Generator (more than 25 KVA) |
82 |
No |
50 % |
Gradall |
85 |
No |
40 % |
Grader |
85 |
No |
40 % |
Horizontal Boring Hydraulic Jack |
80 |
No |
25 % |
Hydra Break Ram |
90 |
Yes |
10 % |
Impact Pile Driver (diesel or drop) |
95 |
Yes |
20 % |
Insitu Soil Sampling Rig |
84 |
No |
20 % |
Jackhammer |
85 |
Yes |
20 % |
Mounted Impact Hammer (hoe ram) |
90 |
Yes |
20 % |
Paver |
85 |
No |
50 % |
Pickup Truck |
55 |
No |
40 % |
Pneumatic Tools |
85 |
No |
50 % |
Pumps |
77 |
No |
50 % |
Rock Drill |
85 |
No |
20 % |
Scraper |
85 |
No |
40 % |
Slurry Plant |
78 |
No |
100 % |
Slurry Trenching Machine |
82 |
No |
50 % |
Soil Mix Drill Rig |
80 |
No |
50 % |
Tractor |
84 |
No |
40 % |
Vacuum Excavator (vac-truck) |
85 |
No |
40 % |
Vacuum Street Sweeper |
80 |
No |
10 % |
Vibratory Concrete Mixer |
80 |
No |
20 % |
Vibratory Pile Driver |
95 |
No |
20 % |
Welder |
73 |
No |
40 % |
NOTES:
- (a) Measured at 50 feet from the construction equipment, with a "slow"
(1 sec.) time constant.
- (b) Noise limits apply to total noise emitted from equipment and
associated components operating at full power while engaged in its
intended operation.
- (c) "Impact" equipment is assumed to produce separate
discernable sound pressure maxima.
- (d) "Acoustic Usage Factor" represents the percent of time
that equipment is assumed to be running at full power while working on
site
TABLE 3. NOISE MONITORING LOCATIONS (See Also Figure 1)
CA/T LOCATION NO. |
LOCATION/ADDRESS |
LAND USE |
TO BE DEVELOPED SPECIFICALLY FOR EACH CONTRACT
TABLE 4. ADJUSTMENTS FOR EQUIPMENT NOISE MEASUREMENTS AT LESS THAN
50 FEET
Measurement
Distance (Feet) |
Values to be Subtracted from Measured
Noise
Level to Estimate Noise Level at 50 Feet (dBA) |
19-21 |
8 |
22-23 |
7 |
24-26 |
6 |
27-29 |
5 |
30-33 |
4 |
34-37 |
3 |
38-42 |
2 |
43-47 |
1 |
48-50 |
0 |
TABLE 5. BACKGROUND NOISE LEVELS AND CORRESPONDING LOT-LINE NOISE
CRITERIA
Site
No. |
Receptor
Address |
Background L10 in dBA
Daytime _Evening _Nighttime |
Lot-Line L10 Criteria in dBA
Daytime _Evening _Nighttime |
TO BE DEVELOPED SPECIFICALLY FOR EACH CONTRACT
Notes:
- Daytime is defined as 7 AM to 6 PM
- Evening is defined as 6 PM to 10 PM
- Nighttime is defined as 10 PM to 7 AM
- n/a indicates that data was either not available or criteria limits
do not apply
INSERT CONTRACT- SPECIFIC MAP
INSERT CONTRACT- SPECIFIC MAP
FIGURE 1. SITE MAP & NOISE MONITORING LOCATIONS
NOISE CONTROL PLAN
(duplicate as needed)
PART A: EQUIPMENT INVENTORY
Contract No.: _______________ Contract Name:
_______________________Contractor: ___________________
Site: ______________________ Date: ________________
Resubmit every 6 months
(ATTACH SITE SKETCH)
Code
(a) |
Equipment |
Noise Limit
(dBA)
(f) |
Estimated
Noise at 50' (dBA)
(g) |
Date Begin
(h) |
Date End
(i) |
Daily Use
(j) |
Category
(b) |
Model
(c) |
ID#
(d) |
HP
(e) |
|
|
|
|
|
|
|
|
|
D/E/N |
|
|
|
|
|
|
|
|
|
D/E/N |
|
|
|
|
|
|
|
|
|
D/E/N |
|
|
|
|
|
|
|
|
|
D/E/N |
|
|
|
|
|
|
|
|
|
D/E/N |
|
|
|
|
|
|
|
|
|
D/E/N |
|
|
|
|
|
|
|
|
|
D/E/N |
|
|
|
|
|
|
|
|
|
D/E/N |
|
|
|
|
|
|
|
|
|
D/E/N |
|
|
|
|
|
|
|
|
|
D/E/N |
FIGURE 2. NOISE CONTROL PLAN FORM - PART A
NOISE CONTROL PLAN
(duplicate as needed)
PART B: PREDICTED NOISE LEVELS
Contract No.: ___________________________ Contract Name:
_________________________
Contractor: _____________________________ Site:
__________________________________
Date: __________________________________ Land Use:
_____________________________
Resubmit every 6 months
Time Period |
Calculated Noise Levels (dBA) |
Noise Level Limit (dBA) |
Calculated L10 (dBA) |
Calculated Lmax (dBA) |
L10 Limit (dBA) |
Lmax Limit (dBA) |
Daytime (7AM - 6PM) |
|
|
|
|
Evening (6PM - 10PM) |
|
|
|
|
Nighttime (10PM - 7AM) |
|
|
|
|
NOISE ABATEMENT MEASURES |
ANTICIPATED EFFECTS |
CALCULATIONS - attach additional sheet(s) as
needed
FIGURE 3. NOISE CONTROL PLAN FORM - PART B
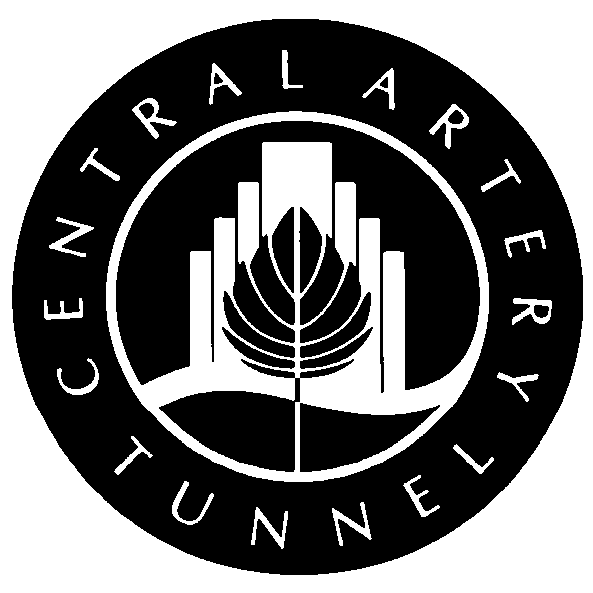 |
Central Artery / Tunnel Project |
CONTRACT NO(S):__________________________
DATE: _____________________________________
TIME:__________________________________ Hrs
(0000 Hrs - 2359 Hrs) |
NOISE MEASUREMENTS
REPORT FORM
MEASURED BY:___________________________________ OF:
________________________________________
(COMPANY)
MONITORING ADDRESS:
__________________________________________________________________
(PROVIDE SKETCH ON BACK)
LOCATION NO:__ N - ____________ WIND
SPEED:_____________ MPH DIRECTION:
________________
LOCATION OF SOUND LEVEL METER: (NO CLOSER THAN 50 FEET FROM EQUIPMENT
AND 5 FEET FROM REFLECTIVE SURFACE)
MONITORING WAS CONDUCTED:__________FEET FROM
EQUIPMENT(___________________________)
(TYPE(S); LEAVE BLANK FOR BASELINE)
LAND USE: o
RESIDENTIAL/INSTITUTIONAL o
BUSINESS/RECREATIONAL o
INDUSTRIAL
SOUND LEVEL METER: MAKE AND MODEL:_______________________________________________
DURATION OF MEASUREMENT:______________________
CALIBRATION LEVEL:_______________________________
|
Noise Level
(dBA) |
Noise Limit
(dBA) |
Lmax * |
|
|
L1 |
|
|
L10 * |
|
|
L50 |
|
|
L90 |
|
|
Leq |
|
|
|
FIELD NOTES
(e.g., 2200-2205 H, AIRPLANE, 90 dBA)
_______________________________________________
_______________________________________________
_______________________________________________
_______________________________________________
_______________________________________________
_______________________________________________
_______________________________________________
_______________________________________________
_______________________________________________ |
(*) indicates required noise measurement data
CHECK ONE OF THE FOLLOWING
o
ONGOING CONSTRUCTION o
POST-CONSTRUCTION:_____________________o
BASELINE CONDITIONS
(CONTRACT)
(COMPLETE ALL THAT APPLY BELOW)
ACTIVE
CONTRACT(S):_____________________________________________________________________
COMPLAINT
RESPONSE:____________________________________________________________________
ABATEMENT FOLLOW
UP:__________________________________________________________________
FIGURE 4. NOISE MEASUREMENTS REPORT FORM
APPLICATION FOR CERTIFICATE OF EQUIPMENT NOISE
COMPLIANCE
Contractor
Name:____________________________________________________________________________
Contract Name &
Number:_____________________________________________________________________
Equipment
Type:_____________________________________________________________________________
Manufacturer & Model
NO.:____________________________________________________________________
Identification
Number:_________________________________________________________________________
Rated Power &
Capacity:______________________________________________________________________
Operating Cond. During
Test:____________________________________________________________________
Measured Lmax Noise Levels and Distance:
- Right Side:_________________ dBA(SLOW), at__________________ feet
Left Side:__________________ dBA(SLOW), at__________________ feet
Adjusted Lmax Noise Levels at 50 Feet:
- Right Side:_________________ dBA(SLOW).
Left Side:__________________ dBA(SLOW).
Equipment Noise Emission Limit (Table 2): _____________ dBA(SLOW)
If equipment noise level exceeds maximum value allowed, indicate
action taken to achieve compliance:
_____________________________________________________________________________________
_____________________________________________________________________________________
- ACOUSTICAL ENGINEER
- Name, Address & Phone
No.__________________________________________________________
ACOUSTICAL ENGINEER
- Authorized Signature: _____________________________________Date:
______________________
-
CONTRACTOR'S CONCURRENCE
- Authorized Signature: _____________________________________Date:
______________________
ENGINEER'S CONCURRENCE
- Authorized Signature:
_____________________________________Date:______________________
FIGURE 5. EQUIPMENT NOISE LEVEL DATA REPORTING FORM